The International Fusion Materials Irradiation Facility – Demo Oriented Neutron Source (IFMIF-DONES) is a single-sited novel research infrastructure for testing, validation and qualification of the materials to be used in future fusion power plants like DEMO (a demonstration fusion reactor prototype). In relation to this international project, in December 2017, Fusion for Energy (F4E) evaluated positively the joint Spain and Croatia proposal to site the IFMIF-DONES in Granada. The facility aims to solve problems associated with use of traditional metallic components due to complex operating conditions with high radiation levels, especially inside the reaction chamber that causes metallic deformities and reduces their mechanical properties.
The upcoming DONES facility in Granada, Spain hopes to achieve testing of these materials using its long Linear Accelerator that accelerates a high-energy beam from its source to 40 MeV at 125 Ma onto a lithium target to generate the required neutron flux which is used to irradiate materials under test.
Within the FusionCAT project, IREC´s fusion technology group (bFUS) has been involved in the design and development of the High Energy Beam Transfer Line (HEBT) and the Beam Dump Transfer Line (BDTL), one of the major sections of the IFMIF-DONES accelerator. bFUS group has been working on the design of the HEBT and BDTL systems and components including the collaboration with industrial partners in Catalonia in order to develop the manufacturing capabilities for related technologies here in Catalonia.
Due to high radiations levels at certain locations, the DONES-IFMIF facility requires remote handling and other systems to perform hand on maintenance, components replacement and alignment without presence of personnel inside the high radiation environment to avoid exposure. For these operations, some of the necessary solutions include:
- Design of remote alignment bench for remote alignment and positioning of HEBT components and assemblies along the axis of the accelerator line.
- Quick disconnection systems for connection of assemblies using robotic manipulator.
- Multi-connection plates for supply of coolant to remote handled assemblies, other electronic sensors and detectors.
- Gripper changer system (GCS) for lifting of assemblies out of the accelerator vault and positioning of the assembly after maintenance.
Few of the other design and manufacturing challenges the HEBT and BDTL design for which industrial collaboration is being searched for:
- Design and manufacturing of scraper and collimators that require thermo-mechanical analysis for heat dissipation and innovative manufacturing methods.
- Manufacturing of Aluminum A-6061 beam tubes of various diameters and thicknesses.
- Design of portable remote handling system for heavy cast iron shielding of scraper.
As previously mentioned, there are several assemblies requiring remote handling; one of which is the lead shutter, an insertable shielding located inside vacuum chambers with the aim to protect against the gamma radiation backscattering. A remote handling design proposal of the lead shutter is shown in Fig. 1.
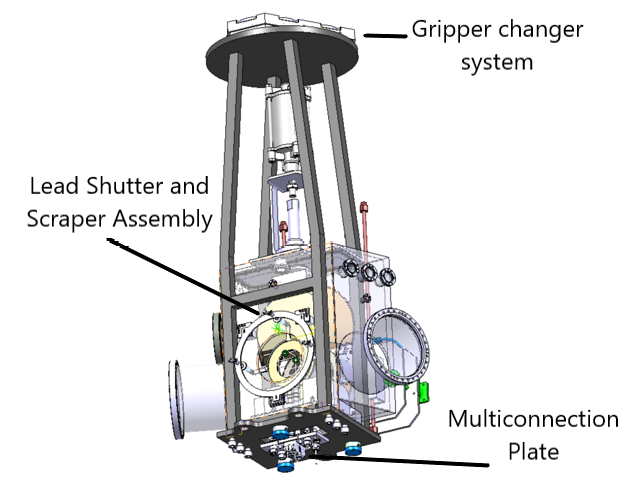
Figure 1 Lead shutter RH assembly design proposal
The multi-connection plates is a component that aids with supply of coolant, power and connects sensors inside of remote handled assemblies to the fixed accelerator systems. bFUS has been collaborating with Stäubli Robotics SA, based in Sant Quirze, for the definition of its design and implementation along the HEBT assembly.
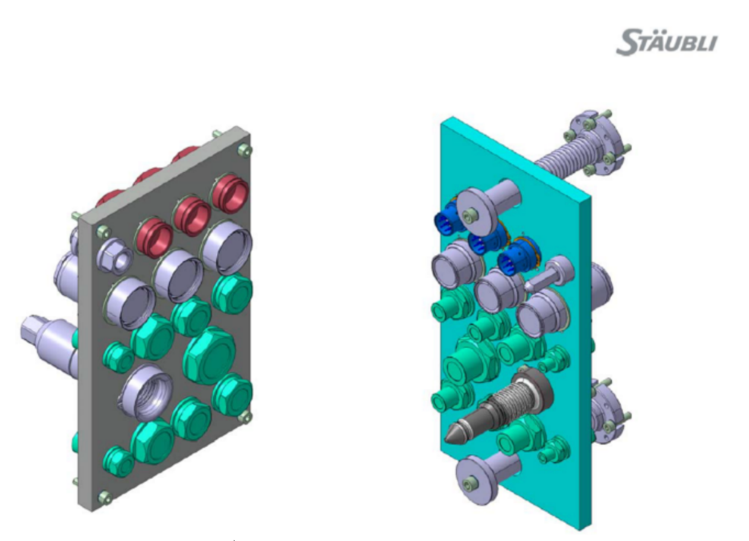
Figure 2 Multi-connection plate from Staubli
The thermo-mechanical design of the components is supported by Eurecat based in Barcelona. This includes the collimator/Scraper, which is a device used to stop drifting particles from their desired trajectory and focus beam and radiation losses in one location, and Beam dump cartridge, which is placed at the core of the beam dump which stops the pulsed beam passing through the beam dump transmission line during commissioning and tuning processes.
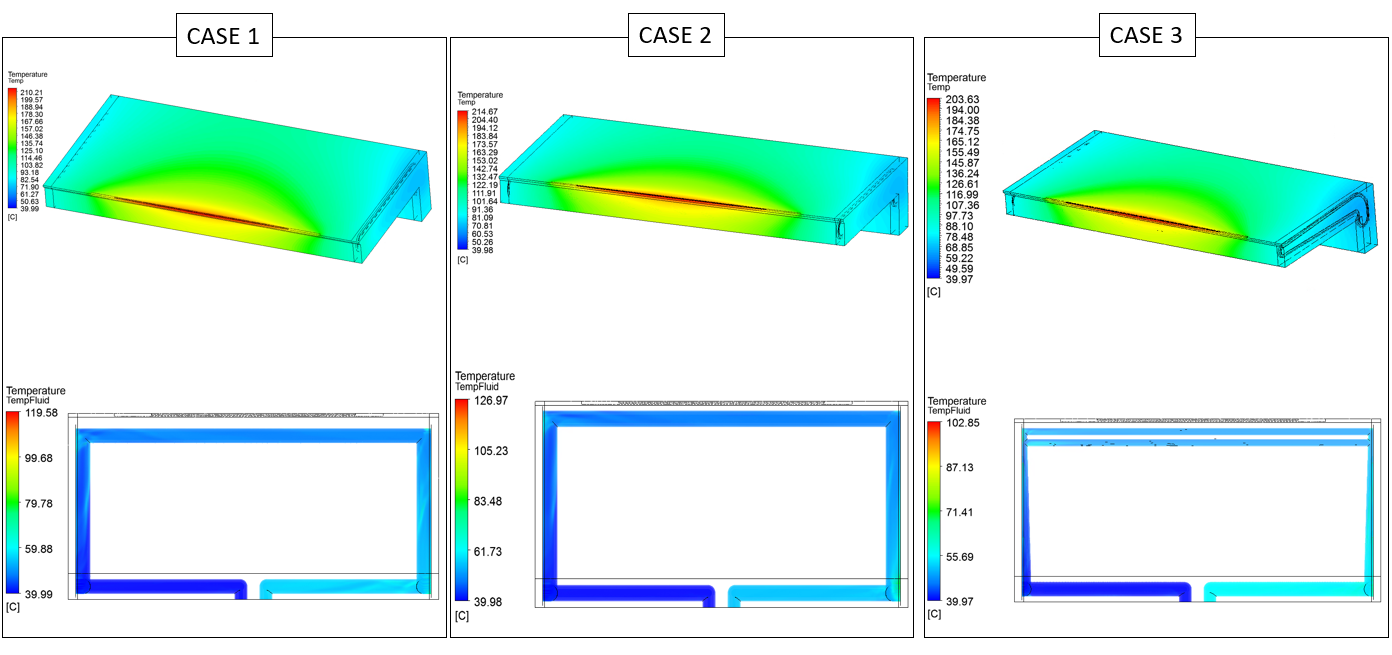
Figure 3 Thermo-mechanical analysis of collimator blade.
Other instances, such as the design of portable hydraulic remote handling assembly for HEBT-Scraper is in discussion with several local manufacturers, one of them being Aresfluid Tecnicas SL based in Barcelona.
A more complex design for which IREC is looking for industrial collaborations is a design of alignment bench with six-degrees of freedom used for alignment with high resolution. Some of the design proposals being considered include Stewart´s platform (Hexapod) and We-plate (CERN, Geneva).
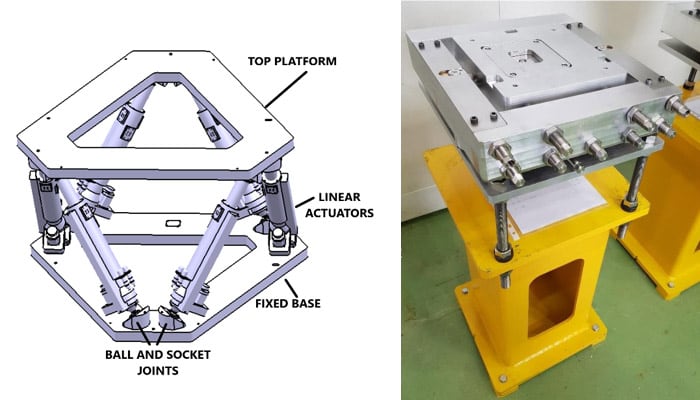
Figure 4 Hexapod(Left) and We-plate(Right)
To summarize, ongoing work on development of fusion technologies at IREC within the FusionCAT project was summarized. Various design challenges and their solutions were briefly described and some ideas about ongoing industrial collaborations were explained. There are still various design solutions under development and for which industrial collaborations are expected. Industrial partners in the field of rapid prototyping, precision machining, development of electro-mechanical components and numerical simulations, would be of great advantage for future project development and design studies. If you are interested in collaboration, please contact bFUS team at ktt@irec.cat.
Fusion is one of the most interesting technologies under research and development and is considered as a possible solution to the climate crisis and achieving the carbon neutrality for the commitments made by the European commission. Hence, being at the fore front of the development of such technologies can not only help Catalonia achieve its energy demands but also, contribute in future development projects across the globe and being a hub for Fusion technology industry’s development.