El laboratorio de catálisis y energía forma parte del grupo de investigación Nanoingeniería de Materiales Aplicados a la Energía (NEMEN) de la UPC. Una de las principales actividades del grupo NEMEN es el desarrollo de catalizadores y reactores catalíticos para la obtención de hidrógeno y el desarrollo de tecnologías relacionadas con el hidrógeno. El grupo NEMEN forma parte del Instituto de Técnicas Energéticas y del Departamento de Ingeniería Química de la Universitat Politècnica de Catalunya.
Uno de los principales retos para desarrollar totalmente los reactores de fusión nuclear es la recuperación de los isótopos de hidrógeno y la separación de éstos de las impurezas generadas en el reactor nuclear. El uso de membranas de Pd para separar el hidrógeno de las posibles impurezas se ha extendido en los últimos años, sin embargo, la presencia de monóxido de carbono (CO) o metano (CH4) estropea las membranas y reduce drásticamente la su vida útil. Por tanto, es necesario encontrar mecanismos que protejan las membranas de Pd para aumentar su durabilidad y eficiencia. En este sentido, el principal objetivo del grupo NEMEN es preparar un catalizador multicomponente que cubra, proteja y mantenga el rendimiento elevado la membrana de Pd haciendo reaccionar y descomponer aquellas impurezas que puedan estropearla y sin que implique un consumo de hidrógeno. Este objetivo forma parte de la tarea 2.4 del proyecto FusionCAT del que el grupo NEMEN forma parte.
La selección y desarrollo de catalizadores multicomponente suponen en sí mismo un reto, dado que las principales reacciones catalíticas necesarias para eliminar la mayoría de impurezas ocurren a diferentes condiciones de temperatura y presión. Por tanto, teniendo en cuenta las principales reacciones y los diferentes catalizadores encontrados en la bibliografía, se han preparado y estudiado diferentes formulaciones de catalizadores para estudiar su viabilidad.
En química, el soporte de un catalizador, normalmente un sólido con una elevada área superficial, donde el catalizador se encuentra adherido. El soporte puede ser catalíticamente inerte, pero frecuentemente contribuye de forma significativa en las reacciones catalíticas. Por lo tanto, no sólo es importante encontrar el soporte adecuado para cada catalizador, sino también maximizar su área superficial. Los principales materiales analizados para ser empleados como soporte son aquellos basados en la ceria (CeO2), la alúmina (Al2O3), la circonia (ZrO2) y el óxido de lantano (La2O3) y los metales níquel (Ni), hierro (Fe) y rodio (Rh) como fases activas. En la tabla 1 se muestran los catalizadores preparados, así como el porcentaje en peso (%wt) de fase activa y los precursores estudiados.
Catalizador | Fase activa (% wt.) | Precursores soporte | Precursores fase activa | |
---|---|---|---|---|
1 | NiFe/CeLaOx | 15% Ni, 3% Fe | Ce(NO3)3, La(NO3)3 | Fe(NO3)3, Ni(NO3)2 |
2 | NiFe/AlCeZrLaOx | 15% Ni, 3% Fe | CeCl3, ZrOCl2, Al(OH)3, La(NO3)3 | Fe(NO3)3, Ni(NO3)2 |
3 | NiFeRh/AlCeZrLaOx | 14,6% Ni, 2,9% Fe, 1,5% Rh | Fe(NO3)3, Ni(NO3)2, RhCl3 | |
4 | Rh/AlCeZrLaOx | 1,5% Rh | CeCl3, ZrOCl2, Al(OH)3, La(NO3)3 | RhCl3 |
Tabla 1: Catalizadores preparados.
En la Figura 1 se muestra el sistema de reacción diseñado para evaluar la viabilidad de los distintos catalizadores bajo diferentes condiciones de presión y temperatura. El sistema consiste en cuatro líneas de gas (CO, O2, H2 y CH4) conectados a controladores másicos y una línea líquida (H2O) conectada a una bomba de inyección de un cromatógrafo líquido de alta eficacia (HPLC). Todas las líneas se encuentran calefactadas y conectadas a válvulas antirretorno antes de entrar en el reactor. El reactor está situado en un horno de alta temperatura regulado por un controlador de temperatura (±0,1 °C) y un termopar. A la salida del reactor se han conectado un filtro, una válvula para regular su presión y un manómetro. Asimismo, los gases salientes del reactor se hacen pasar por un condensador y posteriormente se analizan cada 5 minutos en un cromatógrafo de gases durante el transcurso del experimento. La cama catalítica se ha mantenido constante y uniforme a 0.6 cm3 con dilución con carburo de silicio durante todos los experimentos realizados.
Figura 1: Esquema del sistema de reacción empleado.
Las muestras antes y después de reacción se analizaron mediante difracción de rayos-X (XRD) y espectroscopia Raman para determinar las fases cristalinas presentes. Para determinar el estado de oxidación de los elementos presentes se empleó la espectroscopia de fotoelectrones emitidos por rayos X (XPS). Por último, se analizó el comportamiento catalítico de los diferentes catalizadores. La figura 2 muestra conversión de monóxido de carbono (CO) en función de la temperatura para todos los catalizadores preparados. Los resultados muestran cómo los catalizadores basados en los óxidos de Ce/Al/Zr/La y fase activa de los metales Ni/Fe o Ni/Fe/Rh muestran una conversión completa en un intervalo amplio de temperaturas.
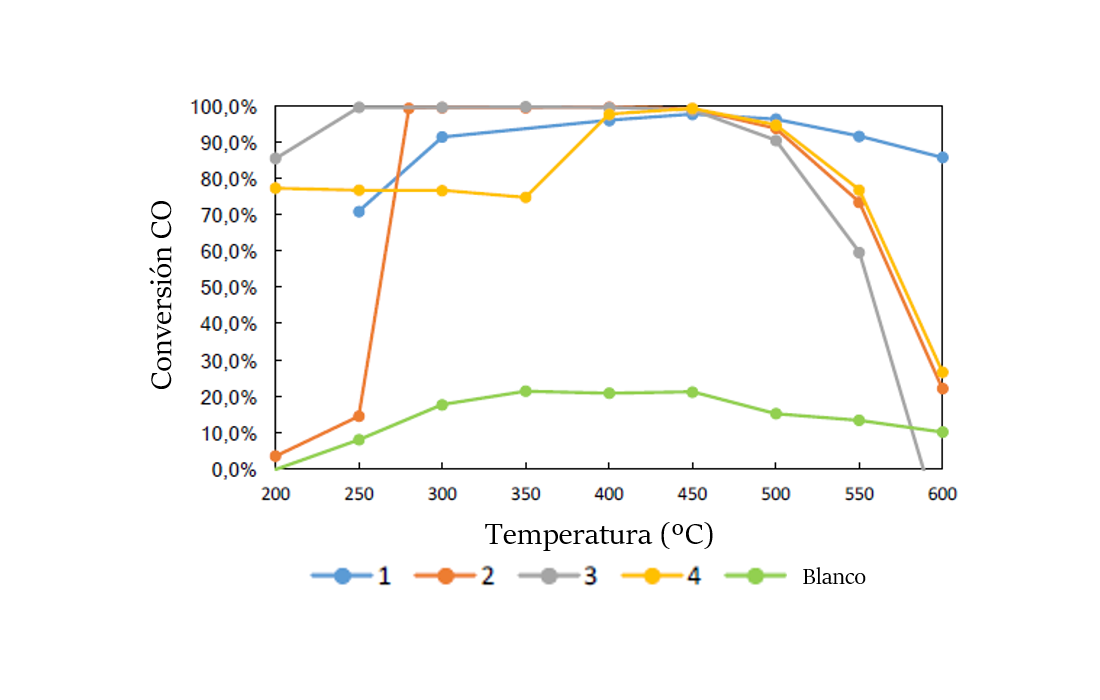
Figura 2. Evolución de la conversión de CO en función del catalizador utilizado y la temperatura de reacción.
El próximo paso es desarrollar un reactor catalítico de membrana (CMR), con una membrana formada por una aleación de Pd, en la que integrar los catalizadores estudiados en forma de pellets y estudiar su comportamiento en función de la presión y la temperatura.