In a previous part of this series of FusionCAT articles, Contribution of the Electrochemistry Laboratory of IQS to FusionCAT project: Hydrogen sensors, different solutions for hydrogen isotopes quantification were proposed. These solutions were based on perovskite-type technical ceramics, like BaCe0.6Zr0.3Y0.1O3-α. The proposed sensors are based on one-end closed tube geometries.
This geometry is notable for having a larger surface area and, therefore, a better response. Thus, once the ceramic material is available, we need fabrication methods that allow the manufacture of small batches of elements with this geometry. There are traditional technologies that can do this work, like slip casting. The main problem with this technology is that the process is manual and not very reproducible. Other traditional systems are the cold isostatic pressure (CIP), but this system needs final machining, which implies an extra material cost, and there is the risk that the piece brakes during the machining process.
IQS proposes the shaping of these ceramics using 3D printing techniques. These technologies, unlike traditional systems, allow the manufacture of pieces through a much more reproducible process. There are multiple 3D printing technologies for ceramic materials shaping. The most used techniques are binder jetting, selective laser sintering, stereolithography and ceramic paste extrusion. At IQS, we selected stereolithography and ceramic paste extrusion due to their characteristics.
Stereolithography
Stereolithography is a technology that can manufacture pieces by the UV polymerization of photosensitive resins with the ceramic powder dispersed layer by layer. Thus, the resolution of the pieces is determined by the resolution of the projection.
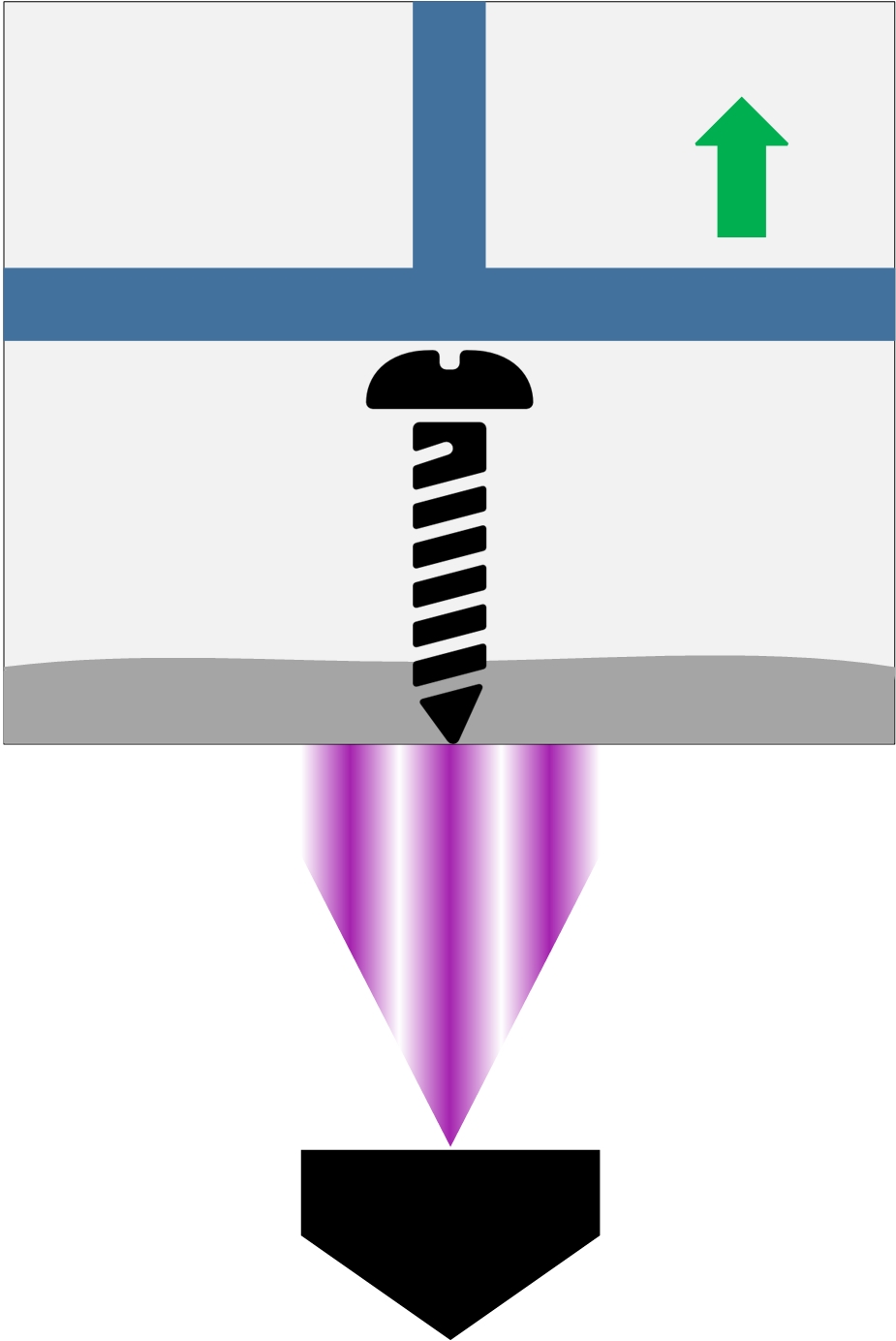
Figure 1. Schematic representation of a 3D system based on stereolithography.
Advantages:
+ High-resolution pieces with high fidelity to the initial model + It can print multiple pieces simultaneously |
Disadvantages:
– High organic matter content: Difficult to achieve full densification – Price of the instruments |
Extrusion of ceramic pastes
The extrusion technology of ceramic pastes can manufacture using a viscous paste of organic components, like binders, mixed with ceramic powders.
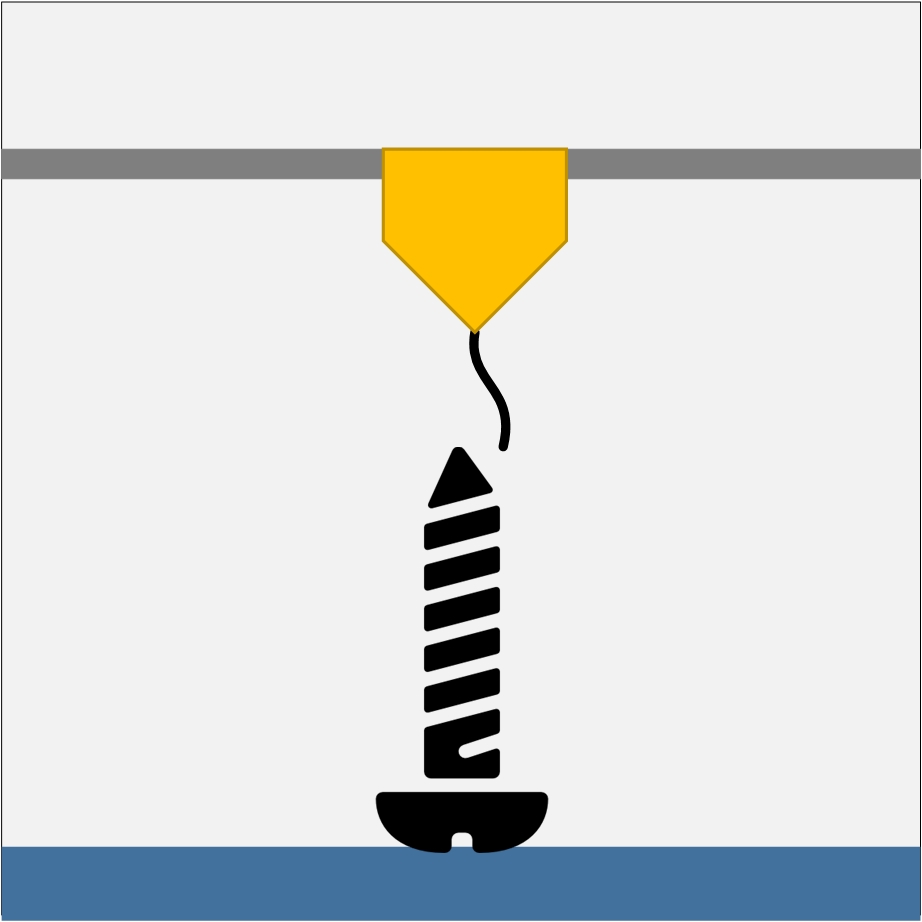
Figure 2. Schematic representation of a 3D ceramic paste extrusion system.
Advantages:
+ Widely used technology and, therefore, low cost. + It needs a low quantity of ceramic powder to operate |
Disadvantages:
– Intermediate resolution due to layers visibility – High organic matter content: difficult to achieve full densification |
At IQS, two traditional technologies have been evaluated: slip casting and Cold Isostatic pressure (CIP), in collaboration with Nanoker S.L., and two 3D printing techniques: stereolithography, in collaboration with Lithoz GmbH, and ceramic pastes extrusion.
Regarding traditional technologies, the slip casting results have presented several reproducibility problems and difficulties to obtain the desired geometry. These pieces have not shown adequate properties for their use in sensors construction. In contrast, with CIP we could obtain the desired geometry. However, the piece thickness was too large, as the material was not able to withstand the stress during the machining process.
The results obtained with 3D printing technologies have been significantly better. The pieces obtained with stereolithography have shown great reproducibility and very thin wall thicknesses. In contrast, the pieces obtained with extrusion presented some limitations: first, the closed part of the tube should be shaped as an ellipse, since the filament was too thin to be shaped as a sphere. Secondly, the pieces could not be too high because they collapsed during the manufacturing process. Finally, since the filament diameter was 1 mm, the joint between layers was still visible. Despite all these problems, once the method was well established, the pieces showed good reproducibility. Images of the pieces obtained with each technology are shown in the next figure:
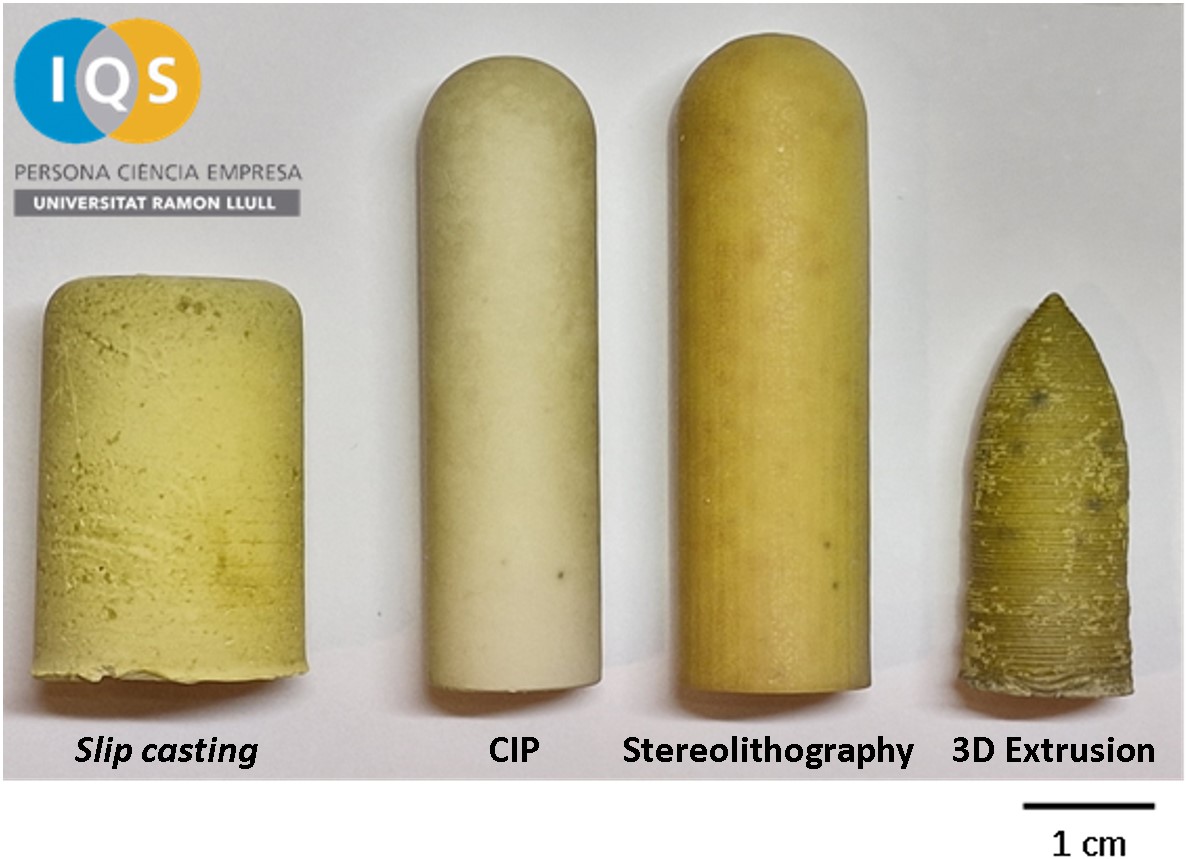
Figure 3. Pieces shaped using (from left to right): slip casting, CIP, Stereolithography and 3D extrusion
The first sensors have been constructed using pieces manufactured by 3D printing (Stereolithography and 3D extrusion) and the experimental campaign has started. The measurements are being performed inside a high-temperature stainless-steel reactor (up to
600 °C), in hydrogen diluted in argon atmospheres, to determine their analytical properties. A calibration curve obtained with the 3D extrusion sensor is shown in the next figure:
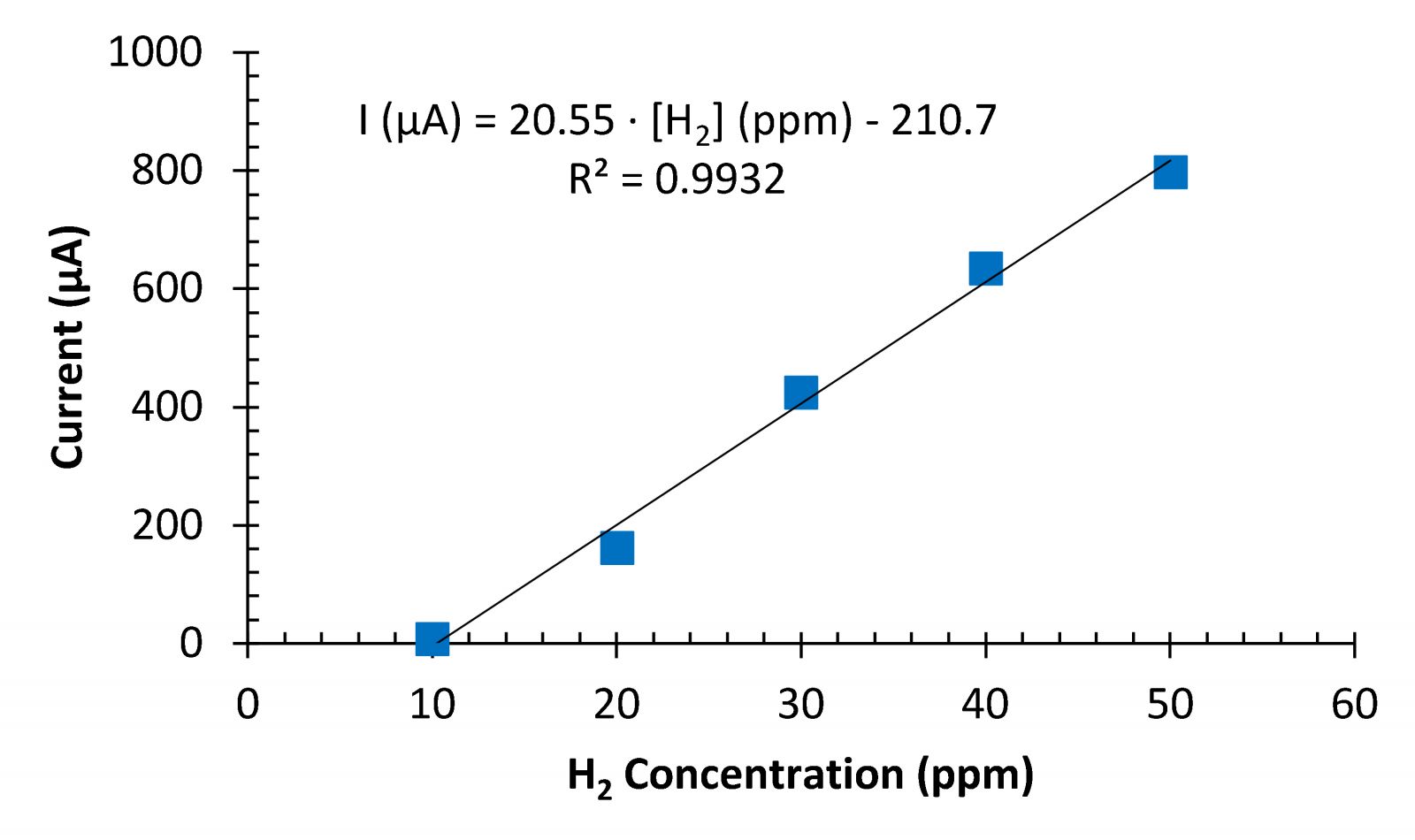
Figure 4. Calibration curve obtained with the sensors manufactured with 3D extrusion
As can be observed in Figure 4, the sensor showed good analytical performance in terms of slope (sensitivity) and linear range. As can be seen, the sensitivity was determined above 20 µA/ppm and the linear range was between 10 and 50 ppm. If these results are compared with sensors constructed with simpler geometries, such as disks, the sensitivity increased from 1.2 to 20.6 µA/ppm (17 times higher) and the linear range was reduced from 60 – 200 ppm to 10 – 50 ppm (between 4 and 6 times lower).
Simultaneously, the preparation of sensors based on CIP-manufactured elements has started, in order to verify if the wall thickness has a significant effect on the sensors’ performance.